Чтобы подписаться, требуется авторизация
Подписчики
0
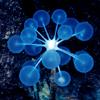
Фрезеровать и гнуть композит
Автор:
Dremel, в Морские самоделки (DIY)
Автор:
Dremel, в Морские самоделки (DIY)
Политика обработки персональных данных